The Development — 997 Intake Manifold Valve Development
At the start of this journey, I thought I had the solution:
“Just use a stronger material for the rod and the failure will be resolved.”
Coming from the software world, I assumed material strength was the root cause. But after examining the failed intake valve rod from my 997 GT3 RS — and consulting a few engineering experts — I realized the truth:
This wasn’t a matter of ultimate strength. It was a textbook case of fatigue failure.
Ultimate Strength: The ultimate strength is the maximum stress that a material can withstand before it breaks or weakens.
Fatigue Failure: a type of mechanical failure where a material weakens and fractures due to repeated or cyclic stress, even when the stress levels are below the material's ultimate strength
The Real Problem: Design, Not Just Material
Once I understood the failure was fatigue-based, I began studying how design geometry — not just metallurgy — affects fatigue resistance. I learned that:
Holes, slots, and sharp corners act as stress concentrators
These areas often become crack initiation zones under vibration or cyclical loading
In an intake valve system — where the rod opens and closes thousands of times — fatigue accumulation is guaranteed
So I sourced a second OEM 997 GT3 RS intake manifold, tore it down, and examined the components.
What I found showcased early damages:
Visible wear in high-stress locations
Surface fatigue already forming, even on an intact rod
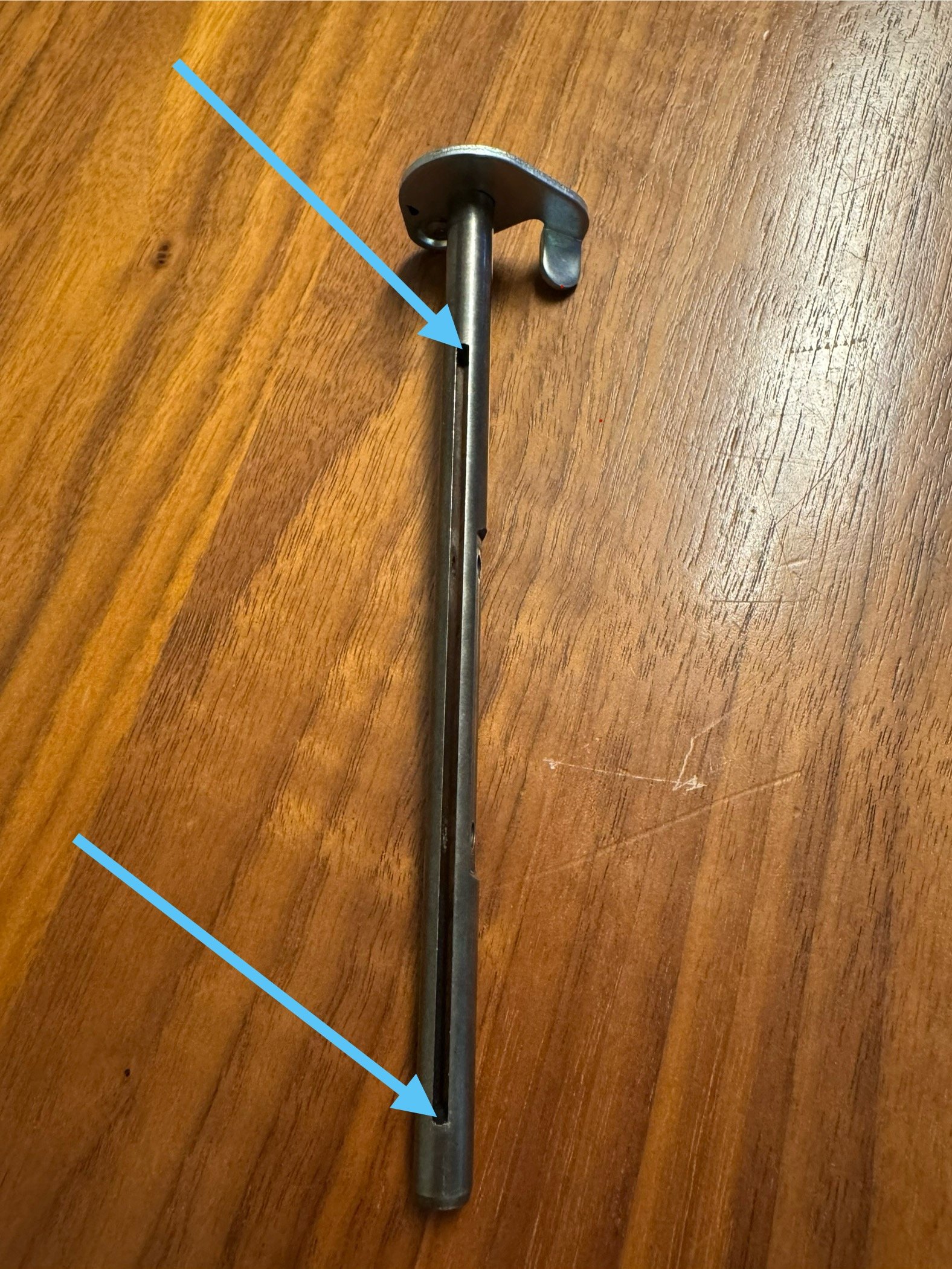
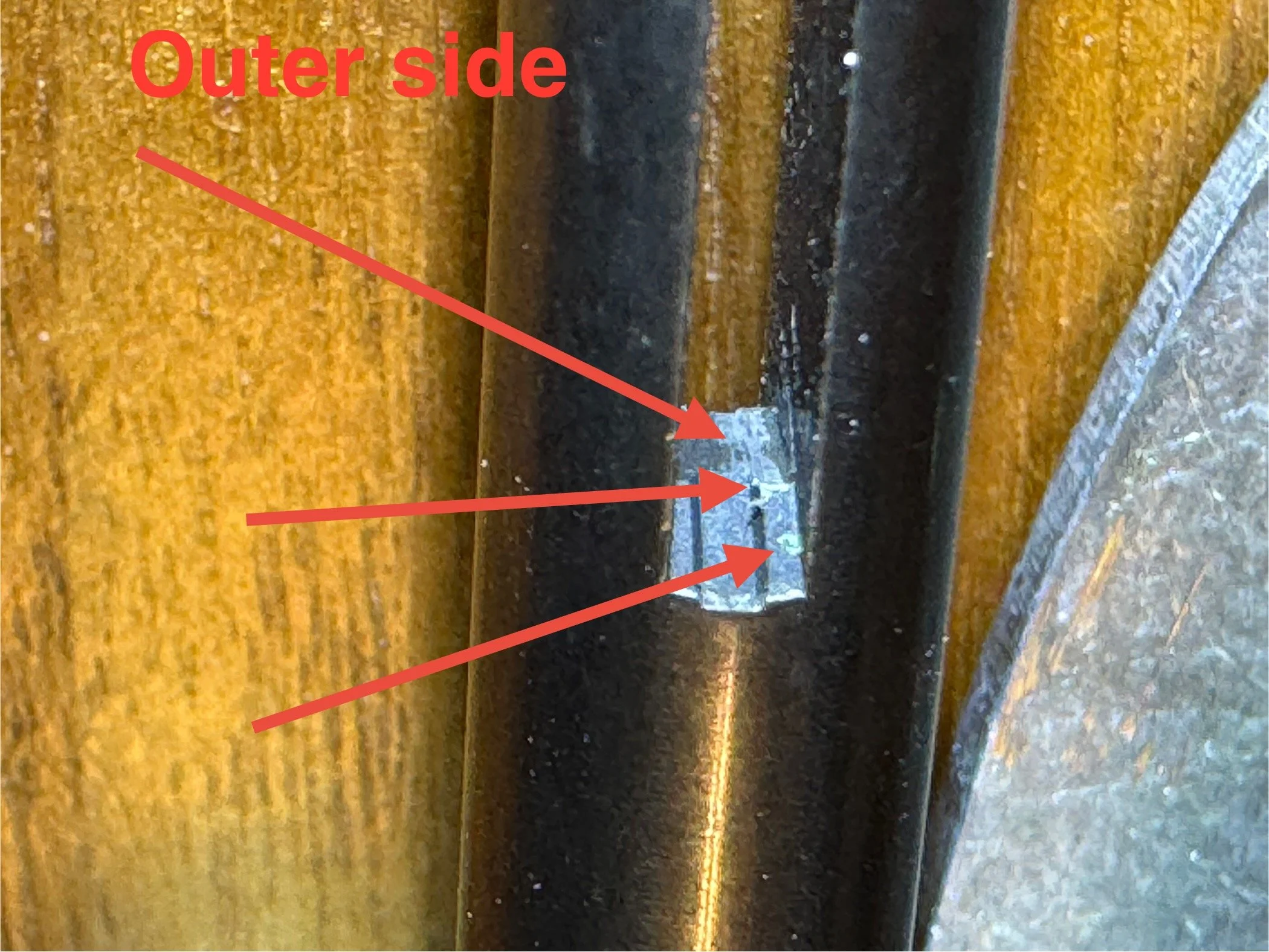
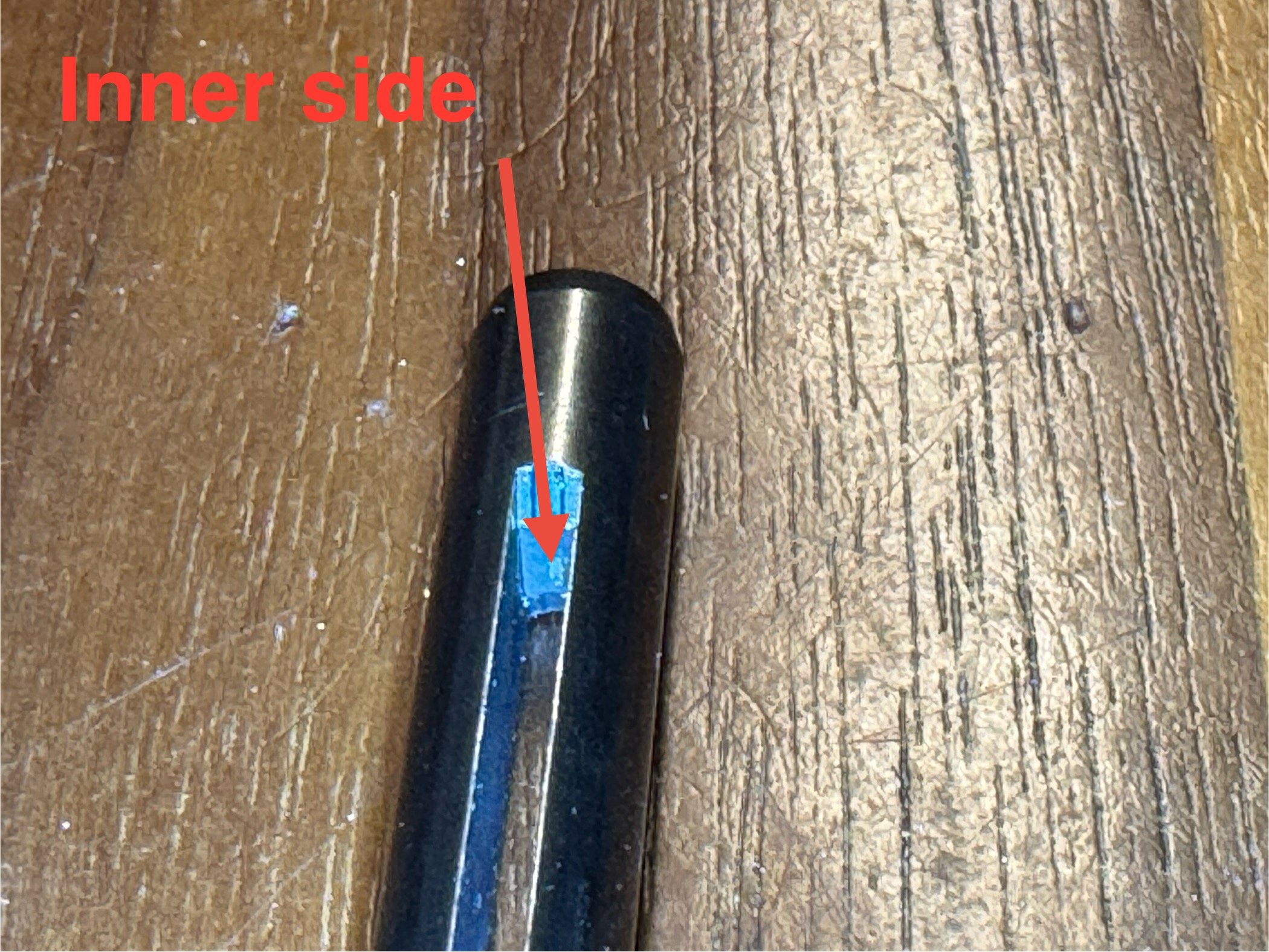
Comparing Porsche Generations: 997 vs 991 vs 718
Knowing that this flaw was likely known to Porsche internally, I investigated how the factory evolved the design over time.
I acquired plenums from:
991 GT3 RS
718 GT4 / Spyder
I disassembled each unit and examined the rod and flap assemblies.
What I found:
Porsche eliminated the holes and slots
The rod diameter increased, improving resistance to bending and vibration
No sharp corners or fatigue-inducing geometry remained
The 991 and 718 rods were clearly clean-sheet designs
I even had all three generations' rods XRF tested to analyze material composition:
The newer generations used similar base steels, but design improvements were clearly the real reason for durability.
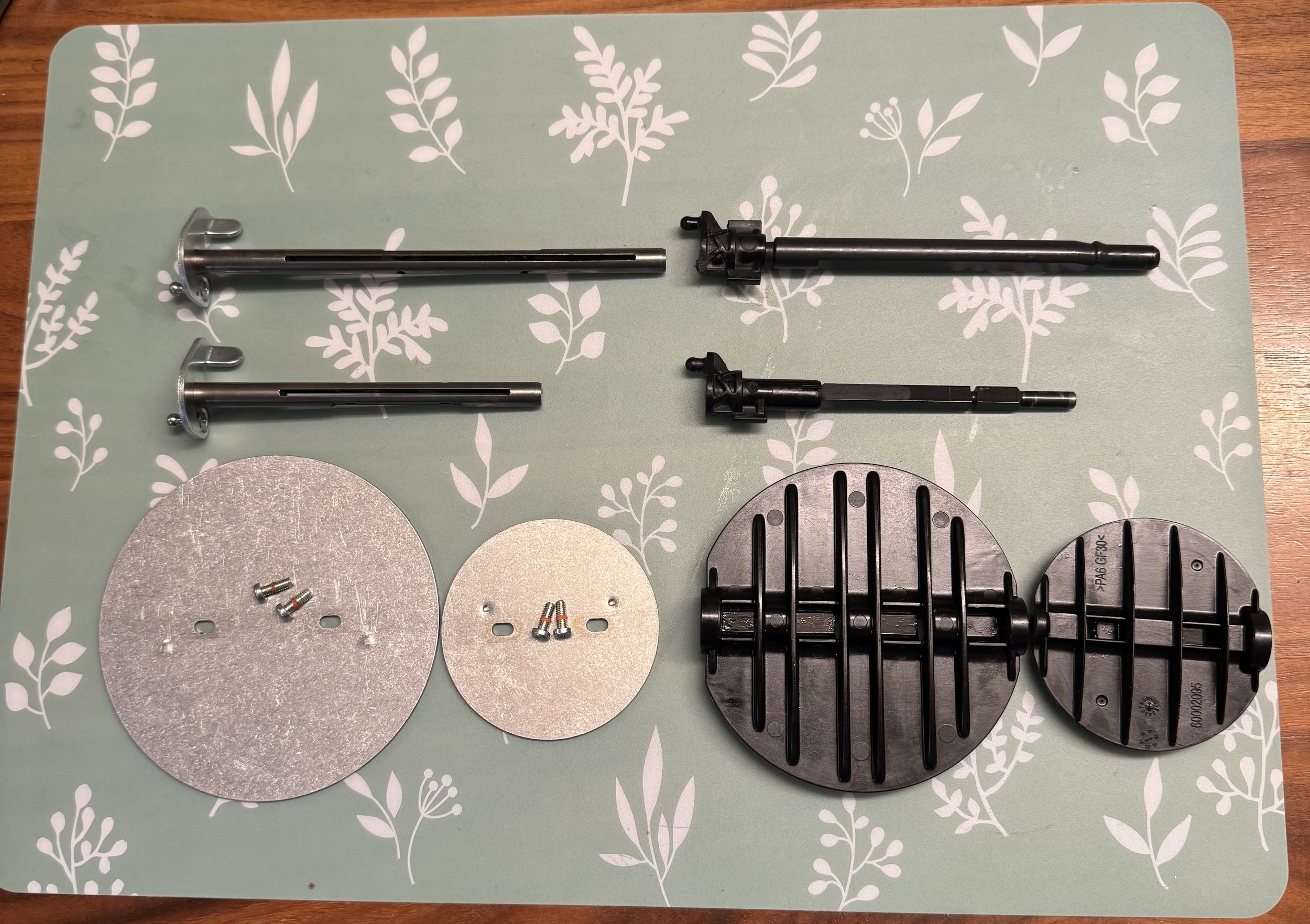

Building the OODA 997 Intake Manifold Valve Kit
Armed with everything I’d learned, I set out to develop the OODA 997 Intake Manifold Valve Kit — a complete, no-compromise redesign of the rod and flap assembly. I drew inspiration from later-generation Porsche GT cars, then pushed the concept further to engineer something explicitly for durability, fatigue resistance, and track use.
Design Goals:
Eliminate all stress concentrators (no holes, slots, or sharp edges)
Upgrade the rod material from 1040 to 17-4 PH stainless steel
Upgrade flap material from Glass-Filled Nylon to Ultem 1000
Increase the rod diameter by 25% for greater stiffness and fatigue margin
Design for drop-in fitment to all 997 GT3 RS intake plenums
Material Selection
Why 17-4 PH Stainless Steel?
17-4 PH was chosen after considering multiple material options, including 4130 and 1040. It offers the best combination of mechanical strength, corrosion resistance, and fatigue endurance — all essential in a component that lives inside a high-vibration, heat-cycled environment like an intake manifold.
Key Advantages:
Superior fatigue resistance — maintains integrity over thousands of cycles
High yield strength — handles vibration and resonance without deformation
Corrosion-resistant — won’t rust or degrade like untreated 1040 steel
Dimensional stability — retains its shape and tolerances long-term
Aerospace pedigree — used in turbine components, structural actuators, and racing applications
Bottom line: 1040 carbon steel was a cost-efficient OEM choice — but not one optimized for longevity. 17-4 PH transforms this component from a known weak point into a long-life, motorsport-ready solution.
Why Ultem 1000 for the Flap?
To complement the metal upgrades, I also redesigned the flap itself — switching from the OEM's Nylon to Ultem 1000, a high-performance thermoplastic used in aerospace and medical applications.
Why Ultem 1000?
Exceptional heat resistance (continuous service temp: 170°C)
Stiff and stable under load, even at elevated temps
Chemically resistant to fuel vapor, oil mist, and manifold deposits
Excellent fatigue endurance and crack resistance
Machinable to high tolerance, ideal for precise sealing and airflow control
Unlike glass-filled nylon — which can absorb moisture, creep under load, and soften at elevated temperatures — Ultem 1000 maintains its structural integrity even under continuous heat soak and high-frequency vibration. While nylon composites are common in OEM applications due to cost and moldability, they can become brittle over time and are prone to dimensional drift in thermally cycled environments.
Together, the 17-4 PH rod and Ultem 1000 flap form a system engineered to survive the conditions that killed the original design — and protect the engine it lives inside.

Bringing It All Together
The result is a fully redesigned, fatigue-resistant rod and valve kit built specifically to:
Solve a known failure in the 997 GT3 RS
Incorporate the best of Porsche’s later designs
Stand up to real-world testing — including my own car, on track
In the final post of this series, I’ll show how the OODA kit performed over:
10+ track days
5,000 street miles
A full teardown inspection for wear, slop, or fatigue damage
This kit is now installed in my own 997 GT3 RS — and I’m trusting it to protect an $80,000 Mezger engine.